Case Study: Automotive Manufacturer Gets A Cost Reduction Alternative
Major automotive OEM reduces plastic bearing weight and cycle time by nearly 60% resulting in significant cost savings.
The Customer's Challenge
This automotive manufacturer needed an affordable, injected molded solution to help reduce the overall weight of the vehicle for fuel economy and cost purposes. In the image below, you will see that the wall of the formerly proposed solution is too thick. Thicker wall sections increase the overall weight of the part, extends its production time, and costs more to produce (see figure below)
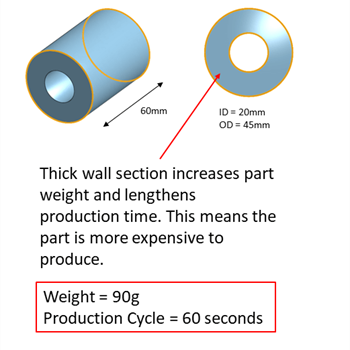
Our Solution
Our team reviewed the customer's drawing and identified potential areas to optimize the bearing design to improve cycle time and weight. With over 70 years of experience in injection molded designs and manufacturing, our team is able to apply our knowledge in bearing production to provide a solution that meets the needs of the automotive OEM manufacturer. Below, you will see our designed solution where the "wall" is made of ribs, rather than one solid piece. The ribs provide strength while reducing the weight, cost, and production time of the part.
Results
From the original design (by a different source) to the design presented, there is a 57% reduction in weight and a 58% reduction in production time. The custom ribbed structure design uses the material manufacturer's recommended wall thickness for the selected material to reduce cooling time in the mold, a large cost driver. The design reduces cycle time and the overall cost of the part.
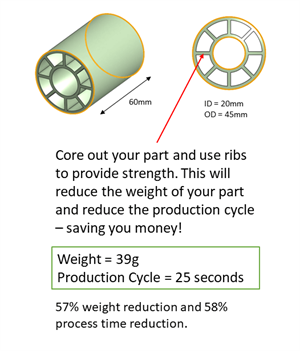
If you are in the market for a custom molded solution to meet the unique needs of your application, get started collaborating with our experts today! Click here to get started.